ball mill limestone particle size

Phone
+86 15538087991


Location
No. 201 Huaxiasanlu road, Pudong, Shanghai, China
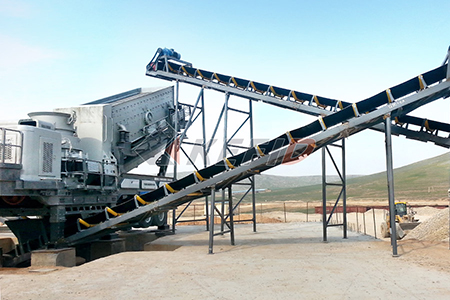
Influences of ball-milled limestone particle sizes and shapes on ...
2020年9月20日 Three distinct filler particle fractions were produced by a planetary high-energy ball mill from limestone aggregates (2.36–4.75 mm). Their particle sizes and shapes were studied by binary image processing and related to milling time and aperture size.
More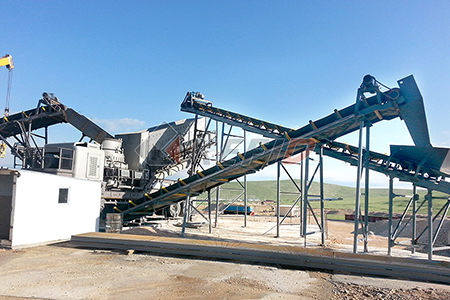
Particle size distribution and structural changes in limestone
2014年1月10日 Based on particle size distribution, it was concluded that the suitable condition for the dry grinding of limestone took place with balls of 10 mm diameter and revolution
More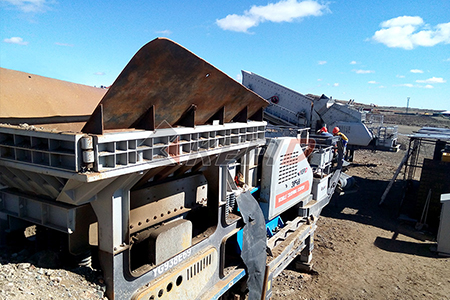
Influences of ball-milled limestone particle sizes and shapes on ...
2020年9月20日 2.1.2. Filler. This study used limestone aggregates from a local quarry with a nominal size range of about 2.36–4.75 mm. The aggregates were ground at room temperature by a planetary high-energy ball mill equipped with a 500 ml ball mill tank and 6 mm- and 10 mm-diameter zirconium oxide balls [21].In order to improve the efficiency of ball grinding, the
More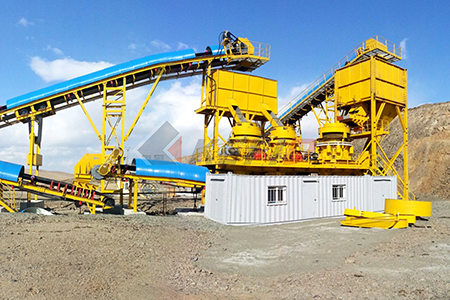
The design and optimization process of ball mill to reduce particle ...
2020年11月16日 The raw materials were ground from the big particle size to the smallest possible by using multistep grinding. In the laboratory, the common method to be used as the ball mill. This work aims to design a simple horizontal ball mill. Calcium carbonate material from limestone and eggshells powder was ground using the developed ball mill.
More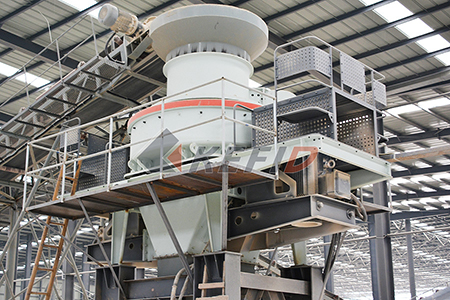
Effect of ball and feed particle size distribution on the milling ...
2018年6月1日 A number of researchers (Deniz, 2012; Bwalya et al., 2014; Petrakis et al., 2016) carried out studies about the effect of feed particle size and grinding media size on the grinding kinetics of different ores.Khumalo et al., 2006 postulated that generally larger sized grinding media would break larger particles quicker but a finer product would be obtained by use of
More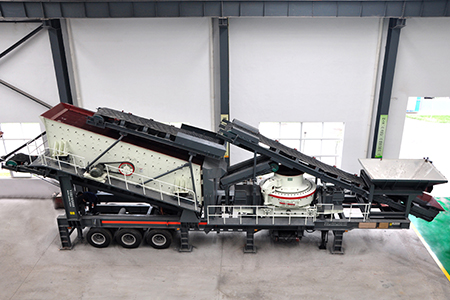
Evolution of grinding energy and particle size during dry ball
2020年10月1日 Evolution of grinding energy and particle size during dry ball-milling of silica sand. Author links open overlay panel Nicolas Blanc a, Claire Mayer-Laigle a ... The onset of particle agglomeration during the dry ultrafine grinding of limestone in a planetary ball mill. Powder Technol., 284 (2015), pp. 122-129. View PDF View article ...
More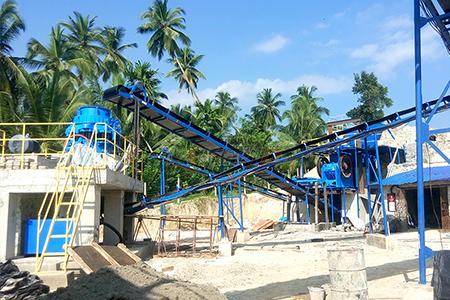
Grinding in Ball Mills: Modeling and Process Control
2012年6月1日 Besides particle size reduction, ball mills are also widely used for mixing, blending and dispersing, amorphisation of materials and mechanical alloying [1, 49, 51].
More
Ball Mill Particle Grinding - Union Process
CL Attritors – Stirred Vertical Ball Mill Limestone Grinding System The economical CL Attritor Stirred Vertical Ball Mill is used for wet grinding limestone for flue gas desulphurization. The process uses limestone feed stock of approximately 6mm in size and wet grinds the limestone to 95% minus 325 mesh. The CL Attritor operates in continuous
More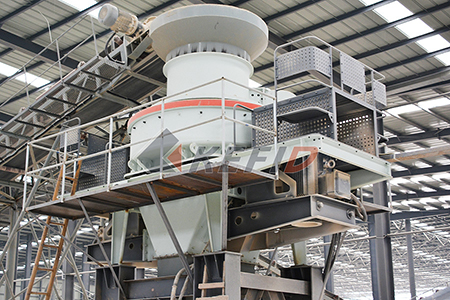
A Technical and Economic Comparison of Ball Mill Limestone
2021年10月13日 A pilot-scale Loesche VRM was used to determine the power required to grind 100 t/h of the same limestone as used at Kusile (work index of 12 kWh/t) with a top size of 19 mm to a 85% and 95% passing 45 µm product. A significant power saving of 39.2% was observed for the dry VRM compared to the wet ball mill (37.7% for the circuit).
More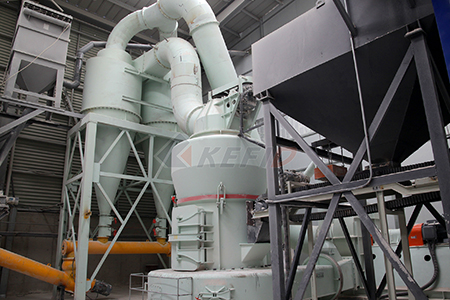
Grinding Media in Ball Mills-A Review - ResearchGate
According to Swart et al. [9], ball mills are mostly used because of their very high size reduction ratio, although they have a very low energy efficiency of about 20%. According to Conger et al ...
More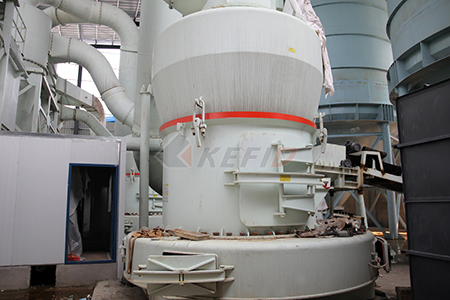
Jet mill grinding of portland cement, limestone, and fly ash:
Request PDF On Nov 1, 2013, Hongfang Sun and others published Jet mill grinding of portland cement, limestone, and fly ash: Impact on particle size, hydration rate, and strength Find, read and ...
More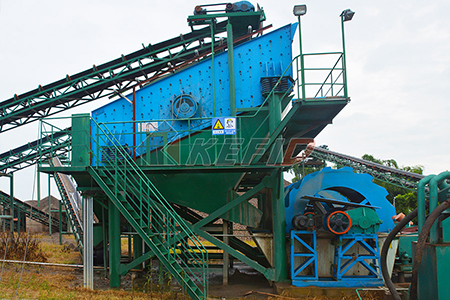
Selected Advances in Modelling of Size Reduction in Ball Mills
2023年9月22日 Table 1 Some examples of variation in the specific breakage rate with grinding time for the limestone ... The value of λ mainly depends on the hardness, specific gravity of the material ground, particle size, and mill ... The Bond model is widely used for the estimation of the mill motor power and the size of ball and rod mills.
More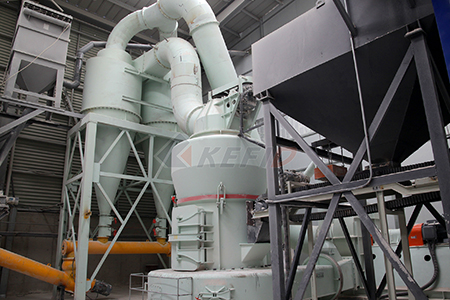
Grinding Media in Ball Mills-A Review - ResearchGate
According to Swart et al. [9], ball mills are mostly used because of their very high size reduction ratio, although they have a very low energy efficiency of about 20%. According to Conger et al ...
More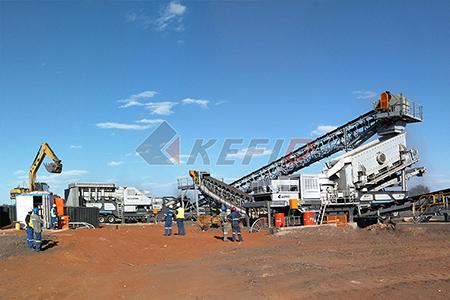
Effect of ball mill grinding parameters of hydrated lime fine
Cumulative under size, % Particle size, µm Fig. 1. Particle size distribution of the feed after the grinding using the ball mill. Table 1 Physical properties of the hydrated lime. d 97 (lm) 853 Median size of the feed (d 50)(lm) 297 Density (g/cm3) 2.24 Bulk density (kg/m3) 690 Whiteness (%) 92.98 Spesific surface area (m2/g) 0.54 Activation ...
More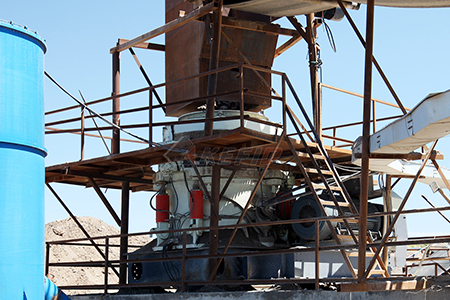
EFFECT OF PARTICLE SIZE DISTRIBUTION ON GRINDING
two sets of wet grinding data (Kim,1974), both on limestone. Malghan ground a 8/10 mesh size fraction of limestone in a ball mill of 20 inch diameter, at 60 percent critical speed using one inch ...
More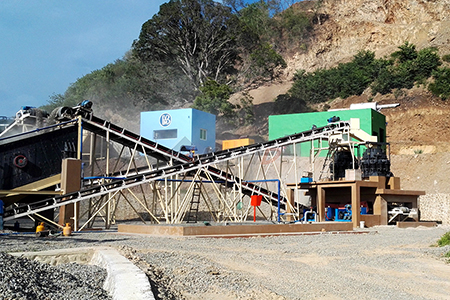
Effect of ball mill grinding parameters of hydrated lime fine
Original Research Paper Effect of ball mill grinding parameters of hydrated lime fine grinding on consumed energy Eyüp Sabaha,⇑, Orhan Özdemirb, Selçuk Koltkaa a Department of Mining ...
More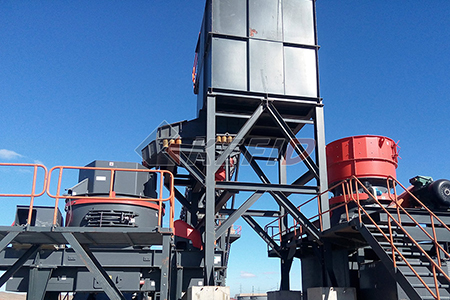
Energy-Model and Life Cycle-Model for Grinding Processes of Limestone
2022年5月22日 The median particle size of stirred ball grinding is X 50 = 17.62 μm for the feed limestone material. After wet grinding of 20 min in the laboratory stirred ball mill, the median particle size of ground limestone is x 50 = 1.76 μm (x 80 = 5.28 μm).
More
Ball Mill Particle Grinding - Union Process
CL Attritors – Stirred Vertical Ball Mill Limestone Grinding System The economical CL Attritor Stirred Vertical Ball Mill is used for wet grinding limestone for flue gas desulphurization. The process uses limestone feed stock of approximately 6mm in size and wet grinds the limestone to 95% minus 325 mesh. The CL Attritor operates in continuous
More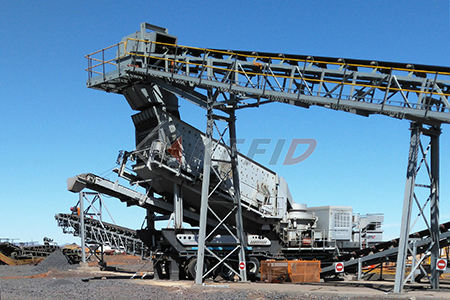
Jet mill grinding of portland cement, limestone, and fly ash:
2013年11月1日 When the jet mill is compared to the ball mill, the jet mill is able to grind materials to a smaller particle size (1–10 μm) with a narrower particle size distribution [5]. The fluidity of jet mill ground cement/limestone mixture and shape of cement particles have been examined [5], and it was found that after jet mill grinding, the fluidity of OPC/limestone pastes
More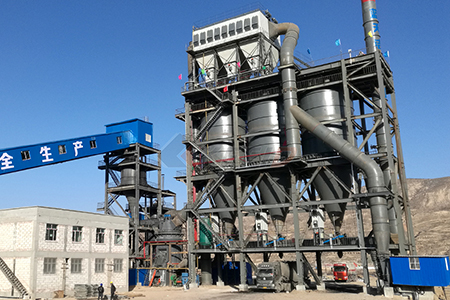
Choosing the Right Laboratory Ball Mills - Union Process
Limestone Slaker Ball Mill (CLS) Small Media Bead Mills (SDM) Wet Grinding Production Mills. ... Starting particle size; Target particle size; Process mode (wet, dry, circulation, batch, continuous) ... Working up to 10 times faster than conventional laboratory ball mills (sometimes referred to as jar mills or pebble mills), ...
More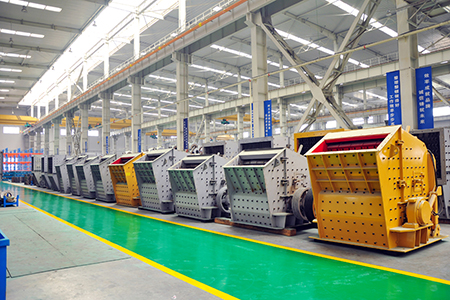
Particle size distribution and structural changes in limestone ground ...
2014年1月10日 The dry grinding of limestone in a planetary ball mill was investigated as a function of the diameter of the grinding balls and the revolution speed of the mill. ... The effects of ball diameter and revolution speed on the mean particle size (d 50) of the limestone ground at different time intervals are shown in Fig. 1.
More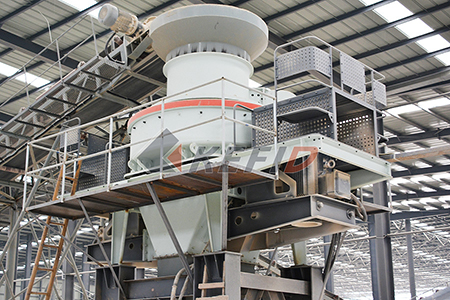
A Technical and Economic Comparison of Ball Mill Limestone
2021年10月13日 A pilot-scale Loesche VRM was used to determine the power required to grind 100 t/h of the same limestone as used at Kusile (work index of 12 kWh/t) with a top size of 19 mm to a 85% and 95% passing 45 µm product. A significant power saving of 39.2% was observed for the dry VRM compared to the wet ball mill (37.7% for the circuit).
More- britadores móveis de esteiras
- la table les meilleurs prix du broyeur humide
- equipos y maquinarias para mineria a cielo abierto
- mais concasseur au Texas sélection de concasseur de calcaire
- fabricant broyeur pour plastique en algerie
- moulin marteaux scm
- raymond moulin whirlwhindconcasseur
- Usine de purification de kaolin en Ouzbékistan
- cylindre de broyage de pierre
- photo de l usine de concassage du calcaire fabrication du sable
- taux de mineraux de 60 tph broyeur de pierres
- broyeur à boulets de roche de phosphate
- usine de concasseur et de l'équipement à vendre
- sable de filtration tunisie
- gabarit minier à haute efficacité