temperature control cement grinding

Phone
+86 15538087991


Location
No. 201 Huaxiasanlu road, Pudong, Shanghai, China
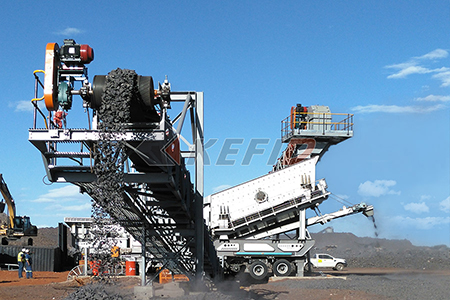
Cement Grinding - Cement Plant Optimization
Controlling parameters are the number of auxiliary blades, the clearance between auxiliary blades and control valve, and the radial position of the main fan blades
More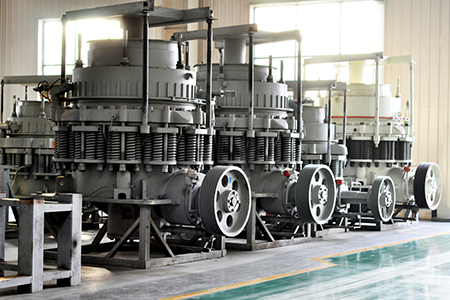
Monitoring Control Systems for Cement Plants - Fuji Electric Global
Enabling stable operations by using optimal electrical equipment and monitoring and control systems to optimally control material processes, fi ring processes, and fi nishing processes.
More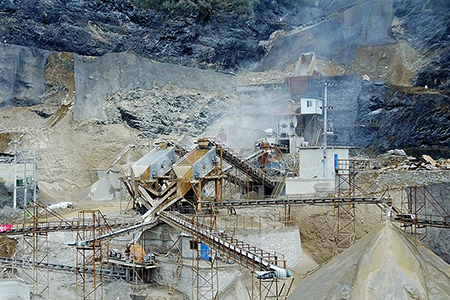
The Cement Plant Operations Handbook - International Cement
raw materials, burning, grinding and quality control are supported by a range of chapters addressing critial topics such as maintenance and plant reporting, alongside a detailed
More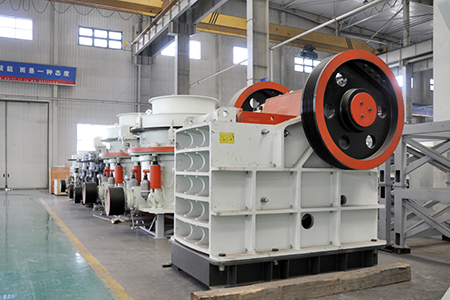
TEMPERATURE MEASUREMENTS IN - Land Instruments International
material and provides an accurate determination of the temperature inside the kiln at that point.
More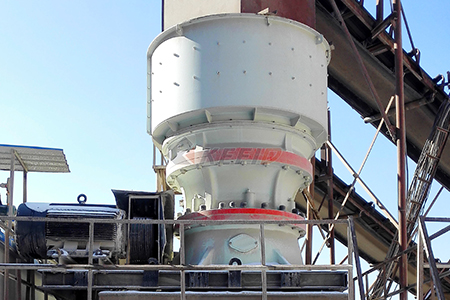
TEMPERATURE CONTROL IN CEMENT MANUFACTURING - Peak
The sheath of the probe can be easily bent and formed into a variety of shapes to suit your application.
More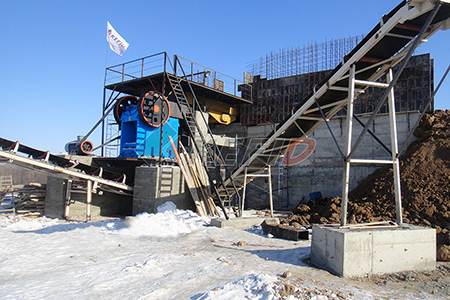
Advanced Process Control for Clinker Rotary Kiln and
2023年3月3日 The design of an internal model control-based PID controller for maintaining the under grate pressure of a grate cooler used in cement plants is presented in, with the goal of achieving target tracking for the considered
More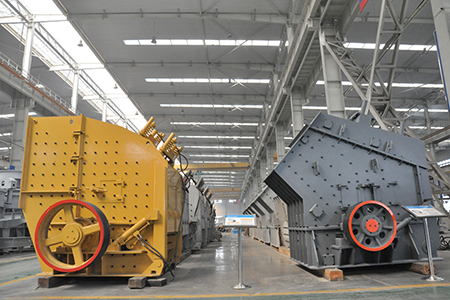
Advanced Control for the Cement Industry - IEEE Control Systems
Furthermore, it was possible to reduce temperature variability, bring the precalciner average temperature toward optimal values, and reduce the risk of cyclone blockages.
More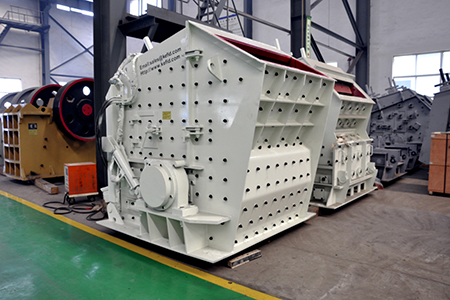
Chapter 4 Cement Manufacturing and Process Control
nd ILC calciner is built into the kiln riser duct. A unique feature of the high-temperature calciner system is the fact that the temperature inside the calciner is independently con-trolled by the
More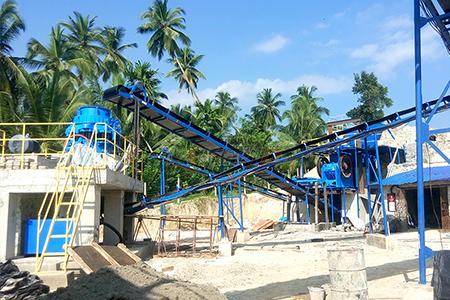
BALL MILLS Ball mill optimisation - Holzinger Consulting
As grinding accounts for a sizeable share in a cement plant’s power consumption, optimisation of grinding equipment such as ball mills can provide significant cost and CO 2
More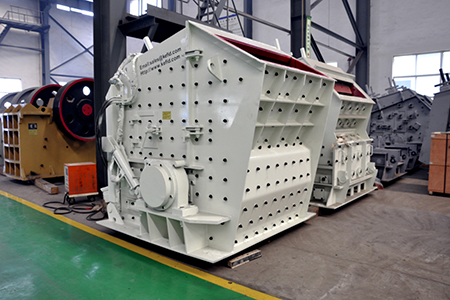
CEMENT GRINDING SYSTEMS - INFINITY FOR CEMENT EQUIPMENT
The final manufacturing stage at a cement plant is the grinding of cement clinker from the kiln, mixed with 4-5% gypsum and possible additives, into the final product, cement . In a modern cement plant the total consumption of electrical energy is about 100 kWh/t . The cement grinding process accounts for approx. 40% if this energy consumption.
More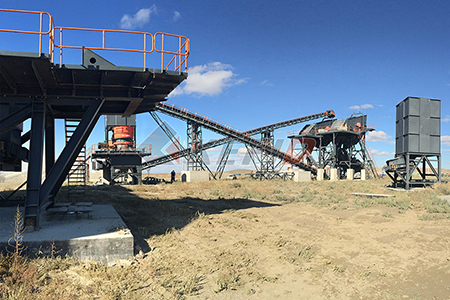
Preparation and action mechanism of temperature control materials for ...
2021年12月20日 Class G high sulfate resistant oil well cement was produced by Sichuan Jiahua Special Cement Co., Ltd, and the main composition is shown in Table 1.The particle size distribution is shown in Fig. 1. Fig. 1 shows that the median particle size D (0.5) of Class G oil well cement is 15.277 μm. SAC was produced by Guangxi Yunyan Special Cement Co., LTD., and
More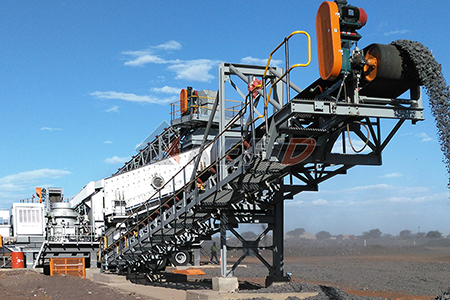
Monitoring Control Systems for Cement Plants - Fuji Electric Global
Cement temperature control at fi nish mill outlet Selection and combination of functions Standard Software functions Cement Finishing Burning ... Preheater induction draft fan (IDF) damper control Control of cement grinding system Clinker and gypsum fl ow control Finish mill monitoring Finish mill separator control Limestone Various raw materials
More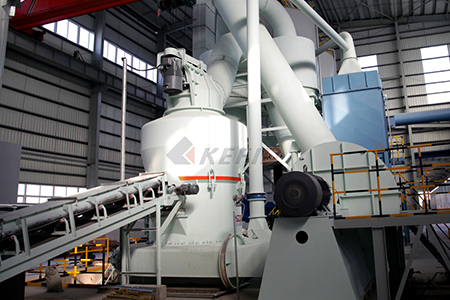
Air Pollution Control in Cement: Solutions Impact
2023年9月22日 Clinkerization and Cement Grinding: Controlling emissions during clinker production and cement grinding. Fly Ash Conveying: Ensuring environmentally responsible handling of fly ash. Packing: Preventing dust emissions during the packaging of cement products. The Transformational Impact of Air Pollution Control Systems
More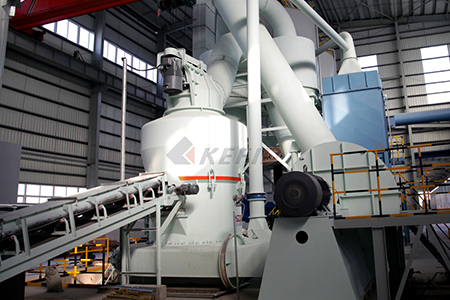
CRUSHING AND GRINDING SEMINAR - The Cement Institute
CEMENT GRINDING COURSE; CEMENT KILN TECHNOLOGY COURSE; CEMENT KILN MAINTENANCE COURSE; CEMENT KEY PERFORMANCE ... Back End Temperature Control – The Three Basic Variables – Target Range for the Three Variables – The Three Basic Conditions – The 27 Conditions (Kurt Peray) – Kiln Slow Down – Normal Operation Procedures on ...
More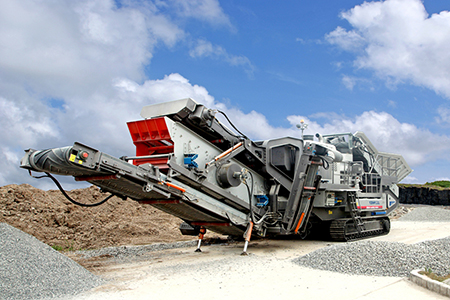
Cement kiln - Wikipedia
Portland cement clinker was first made (in 1825) in a modified form of the traditional static lime kiln. [2] [3] [4] The basic, egg-cup shaped lime kiln was provided with a conical or beehive shaped extension to increase draught and thus obtain the higher temperature needed to make cement clinker.For nearly half a century, this design, and minor modifications, remained the only
More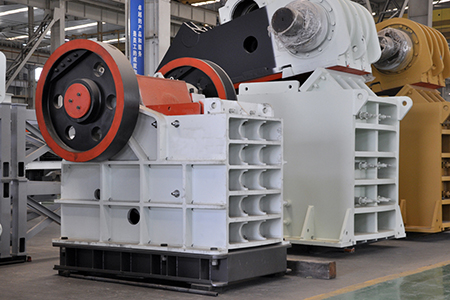
Advanced Control for the Cement Industry - IEEE Control
Temperature (PCT) control solution, on the calciner at Lägerdorf. The technologies used are MPC and MLD. ... productivity of its cement grinding system, consisting of three mills. ABB installed Expert Optimizer on the mills at the Guidonia plant between December 2006 and
More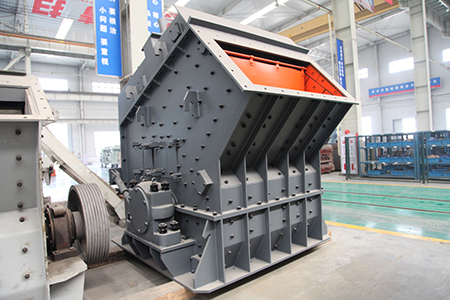
Cement - Extraction, Processing, Manufacturing Britannica
2024年9月26日 There are four stages in the manufacture of portland cement: (1) crushing and grinding the raw materials, (2) blending the materials in the correct proportions, (3) burning the prepared mix in a kiln, and (4) grinding the burned product, known as “ clinker,” together with some 5 percent of gypsum (to control the time of set of the cement).
More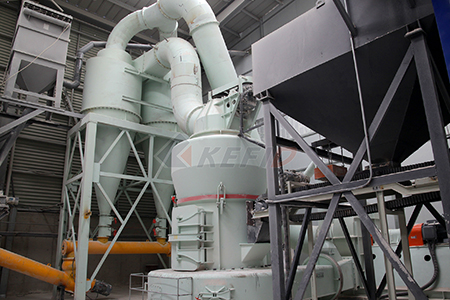
Temperature control: Why it is so important during clinker
It is critical to control the temperature during the cooling of the clinker to ensure the quality of the produced cement and avoid damages. Tel.: +34 951 769 884 info@visiontir Products
More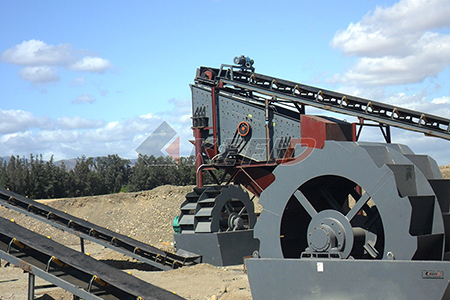
Clinker Grinding Techniques in Cement Manufacturing - JM
2023年10月19日 Consistency and Quality Control: Clinker grinding ensures uniformity in the cement product. It allows for better control over the cement’s properties, including strength, setting time, and durability. Quality control measures are applied during the grinding process to meet specific standards and customer requirements.
More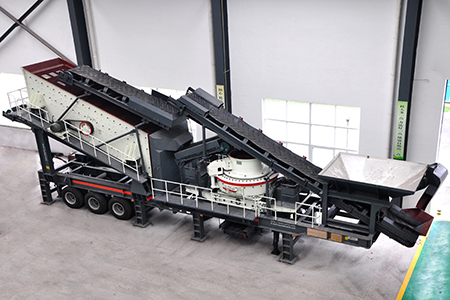
Achieving carbon utilization and storage (CUS) in cement-based ...
2024年9月1日 Utilizing industrial solid waste as a supplementary cementitious material can effectively leverage its potential characteristics while reducing cement consumption and the stockpile of solid waste [10, 11].This can achieve CO 2 emission reduction, but there are actual restrictions on the amount of emission reduction that can be achieved. . Carbonation of solid
More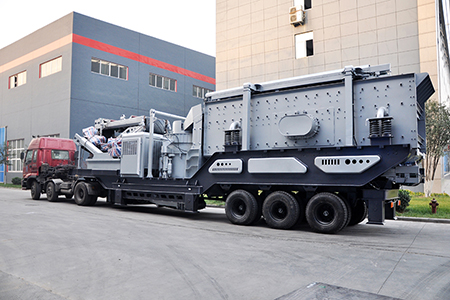
Control in Cement Production - ScienceDirect
1983年1月1日 Cement grinding The control has the following goals: -to produce cement with desired fineness (specific surface and size distribution) -tc maximize the production rate minimizing the ener-gy cost . The grinding consumes a lot of electric energy, this is the highest percentage of the production cost.
More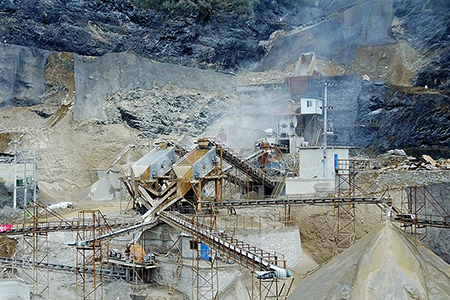
Effects and Control of Chemical Composition of
2020年10月15日 Cement is a substance produced by grinding a mixture of a clay and limestone and heating to a temperature of 1450 ... of interest, has major implications for control of the cement manufacturing ...
More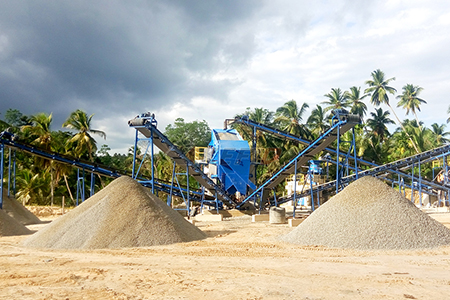
Process control for cement grinding in Vertical Roller
2017年10月1日 The power ingesting of a grinding process is 50-60% in the cement production power consumption. The Vertical Roller Mill (VRM) reduces the power consumption for cement grinding approximately 30-40 ...
More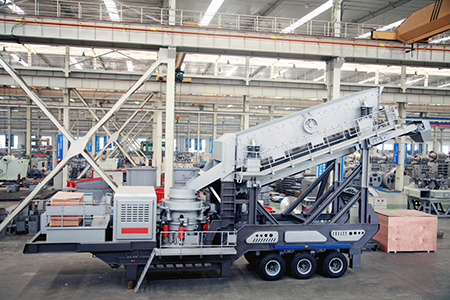
High-level control in cement production World Cement
2020年10月30日 Dirk Schmidt and Eugen Geibel, KIMA Process Control, discuss how the methods of High-Level Control (HLC) have been used in the cement industry in the early 2000s and control ever more complex closed-loop-controlled processes where standard controllers fail.
More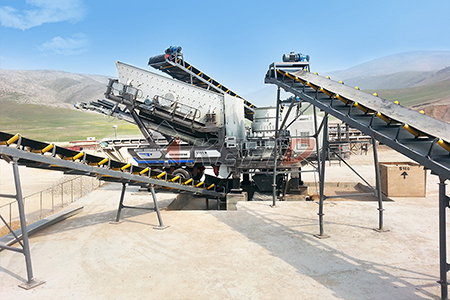
On calciner temperature control algorithm and realization for cement
2001年4月1日 The flow of raw materials in calciner of cement production line with wet-grinding and dry-burning fluctuates in a large range. It can not satisfy the production technical requirements to control ...
More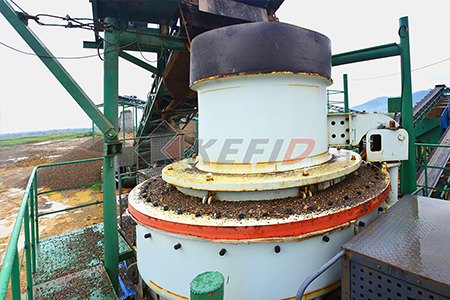
An Introduction to Clinker Grinding and Cement Storage
would be a length of 13.5 m and a diameter of 2.5 m, with a speed of approximately 20 revolutions per minute. Such a mill would normally have a load of approximately 90 tons of grinding media, graduated from 90 mm to 60 mm in the first chamber, 50 mm to 15 mm in the second chamber and 15 mm down in the final chamber.
More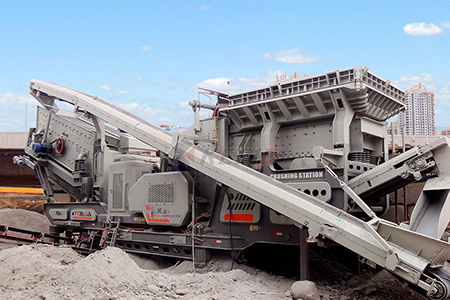
Cement Milling
Cement milling and gypsum dehydration. Because the cement gets hot due to the heat generated by grinding, gypsum can be partly dehydrated, forming hemihydrate, or plaster of Paris - 2CaSO 4.H 2 O. On further heating, hemihydrate dehydrates further to a form of calcium sulfate known as soluble anhydrite (~CaSO 4).
More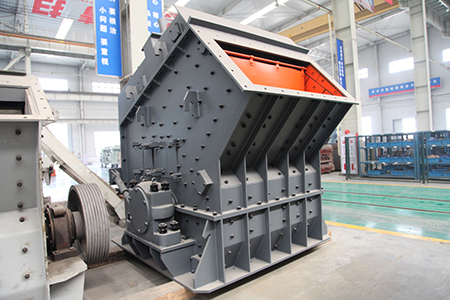
Cement - Extraction, Processing, Manufacturing Britannica
2024年9月26日 There are four stages in the manufacture of portland cement: (1) crushing and grinding the raw materials, (2) blending the materials in the correct proportions, (3) burning the prepared mix in a kiln, and (4) grinding the burned product, known as “ clinker,” together with some 5 percent of gypsum (to control the time of set of the cement).
More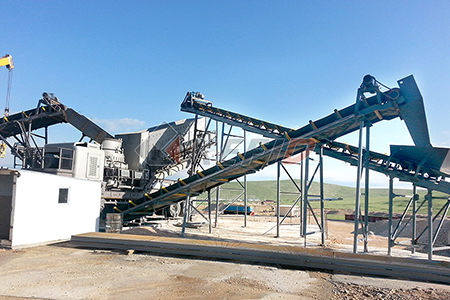
A comprehensive review on Advanced Process Control of cement
2023年1月1日 The clinker produced in the pyro process is pulverised into a fine cement powder during the grinding process ... Design of a generalised predictive controller for temperature control in a cement rotary Kiln. IEEE Lat. Am. Trans., 16 (4) (2018), pp. 1015-1021, 10.1109/TLA.2018.8362131.
More- Broyeurs à billes pour le concassage Lizenithne
- écraser la machine galets
- chargeur de minerai d or de minerai de fer
- Brique Concasseur Location Nottingham À Vendre
- machine de concassage mobile analyse chimique
- comment juger billes phenomènes de surcharge de l'usine
- accidents dans les mines
- Pose de la première concasseur de charbon
- procédé de traitement de sable de silice
- Comment utilisezvous une machine à laver de sable
- broyeur de pierres onan
- meulage de lignite de houille
- broyeur ciment fabrique en algérie
- réducteur de vitesse série mlx broyeur vertical réducteur
- concasseur 15 broyeurs de pierres