cement ball mill design method

Phone
+86 15538087991


Location
No. 201 Huaxiasanlu road, Pudong, Shanghai, China
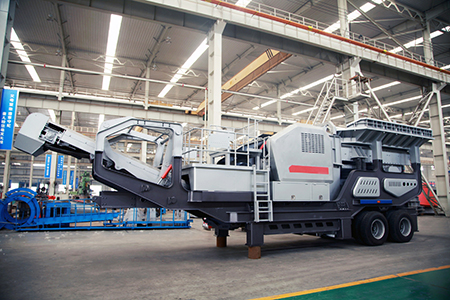
Grinding in Ball Mills: Modeling and Process Control - ResearchGate
2012年6月1日 The paper presents an overview of the current methodology and practice in modeling and control of the grinding process in industrial ball mills. Basic kinetic and energy models of the grinding...
More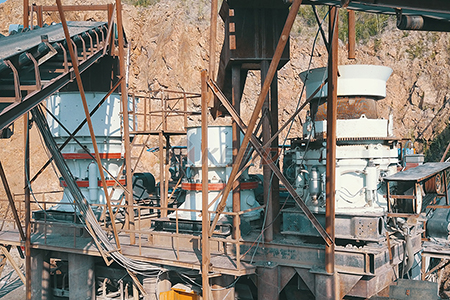
BALL MILLS Ball mill optimisation - Holzinger Consulting
Ball mill optimisation As grinding accounts for a sizeable share in a cement plant’s power consumption, optimisation of grinding equipment such as ball mills can provide significant cost
More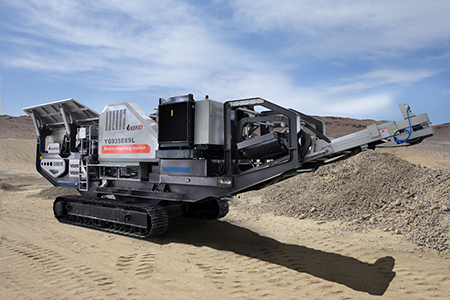
Predictive Controller Design for a Cement Ball Mill
Chemical process industries are running under severe constraints, and it is essential to maintain the end-product quality under disturbances. Maintaining the product quality in the cement grinding process in the presence of clinker
More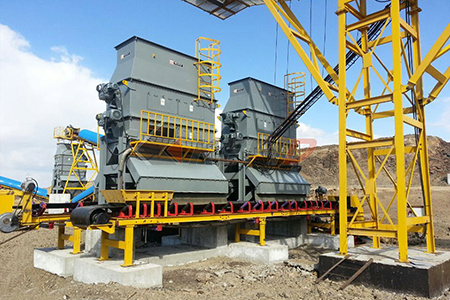
BALL MILLS Ball mill optimisation - Holzinger Consulting
Ball mills and grinding tools Cement ball mills are typically two-chamber mills (Figure 2), where the first chamber has larger media with lifting liners installed, providing the coarse grinding stage, whereas, in the second chamber, medium and fine grinding is carried out with smaller media and classifying liners.
More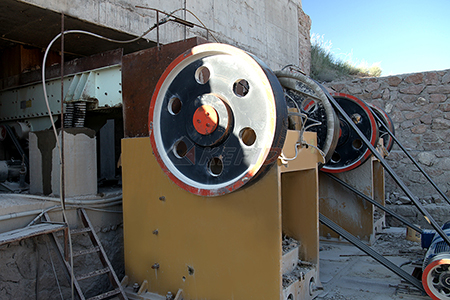
Optimization of Cement Grinding Operation in Ball
Several energy efficient options for cement grinding are available today such as vertical roller mills, roller presses (typically in combination with a ball mill), and clinker pre-grinders with ball mills. Ball mills have been the traditional
More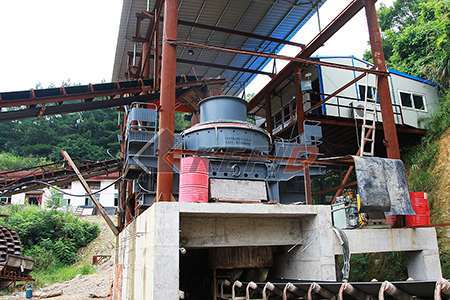
Ball charge optimization - INFINITY FOR CEMENT EQUIPMENT
Previous Post Next Post Contents1 Ball charge optimization2 1 How to use the BP2.1 2 Description of the main indicators used in this BP2.1.0.1 The residue on 2mm/4mm before partition wall2.1.0.2 Material filling level and ball charge expansion2.1.1 Cement mill specific power 1st compartment 2.1.2 Raw mill specific power 1st compartment Ball charge
More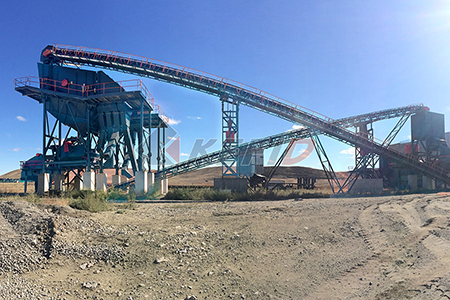
Ball Mill Design/Power Calculation - 911Metallurgist
2015年6月19日 The basic parameters used in ball mill design (power calculations), rod mill or any tumbling mill sizing are; material to be ground, characteristics, Bond Work Index, bulk density, specific density, desired mill tonnage capacity DTPH, operating % solids or pulp density, feed size as F80 and maximum ‘chunk size’, product size as P80 and maximum and finally the
More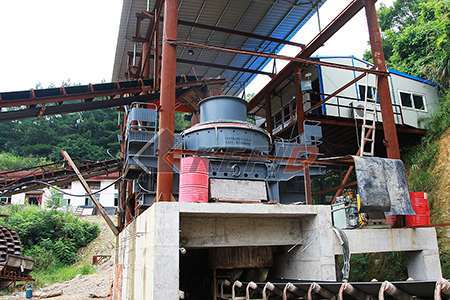
Design and Optimization of Ball Mill for Clinker Grinding in Cement
optimal ball mill performance. In the passing, laboratory- and plant data have been incorporated to carry out set of calculations to quantify ball mill design parametersto reduce energy requirement for clinker grinding significantly as evidenced in Annexure I. These design equations and calculations are of immense help for cement plant personnel.
More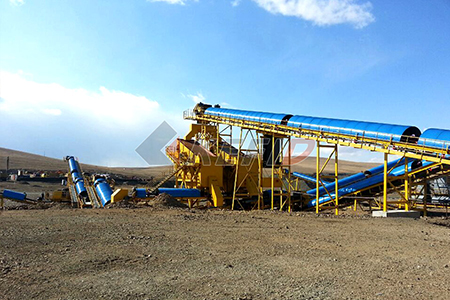
Failure analysis of a ball mill located in a cement’s production line
2022年8月1日 The ball mill understudy has a length of 13.07 m in its cylindrical geometry and a length between supports of 16.2 m (Fig. 1 a,b).The formation of cracks in the middle span has been identified, generally spreading from the holes near the maintenance manhole, as shown in Fig. 1 c. Certified welders carry the repairing procedure using PERMA 622 electrodes [1].
More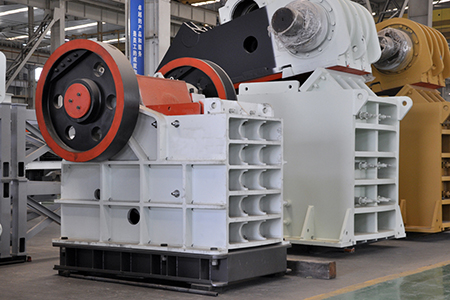
University of Liège - uliege
Discrete Element Method Modeling of Ball Mills-Liner Wear Evolution by Dominik BOEMER ... the shell liner in the first chamber of a 5.8 m diameter cement mill monitored during a decade ... the slightest improvement of the liner design becomes a significant competitive advantage. In general, the liner design depends on its material and its ...
More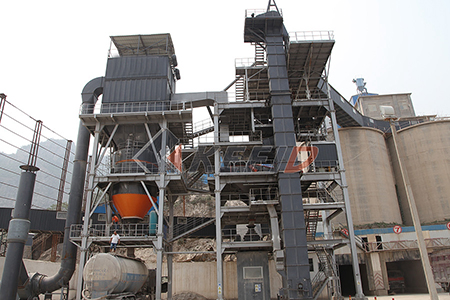
Cement Ball Mill Cost Effective Cement Grinding Mill from AGICO
The installation of liners. Length Diameter Ratio. The length-diameter ratio of the cement ball mill is relatively large. For mills of open-circuit grinding system, the length-diameter ratio is usually between 3.5 and 6 to ensure that the product fineness is qualified through single grinding; For ball mills in closed-circuit grind system, in order to increase the material flow rate, the length ...
More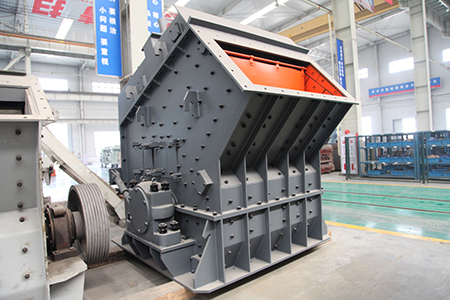
Ball Mill - an overview ScienceDirect Topics
The characteristic tumbling motion of these mills has given them the name ‘tumbling mills’, which include the ball mill, tube mill and rod mill. Ball mills are horizontal rotating cylindrical or conical steel chambers, approximately one third to half full of steel, alloy steel or iron balls, like that shown in Fig. 4.10 A–C , or flint stones.
More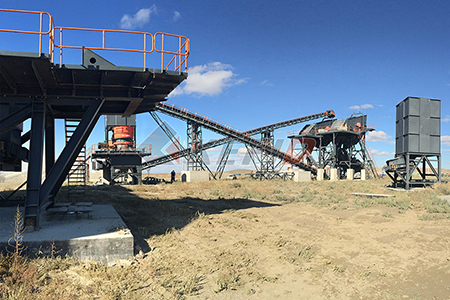
(PDF) Selection and design of mill liners
2006年1月1日 The relining time also reduced by 37.5% with the new liners. Powell et al., 2006; Rajamani, 2006;Yahyaei et al., 2009;Maleki-Moghaddam et al., 2013;Maleki-Moghaddam et al., 2015;Cleary and Owen ...
More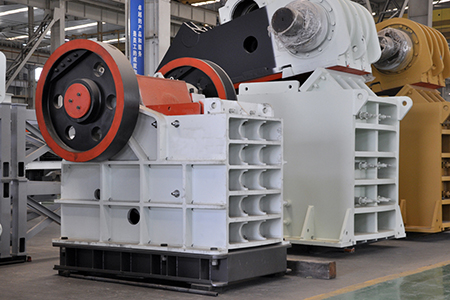
University of Liège - uliege
Discrete Element Method Modeling of Ball Mills-Liner Wear Evolution by Dominik BOEMER ... the shell liner in the first chamber of a 5.8 m diameter cement mill monitored during a decade ... the slightest improvement of the liner design becomes a significant competitive advantage. In general, the liner design depends on its material and its ...
More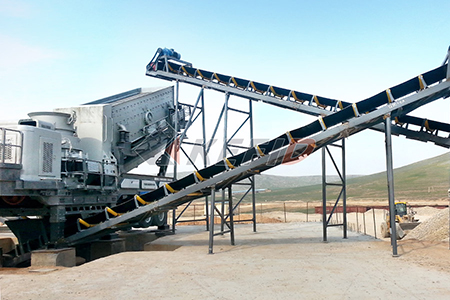
Cement ball mill - DARKO
Method One . For medium and small cement ball mill, Darko Mining Equipment uses an integral frame design. The entire mill is installed on a single welded frame, allowing for installation and debugging within the factory. Once on-site,
More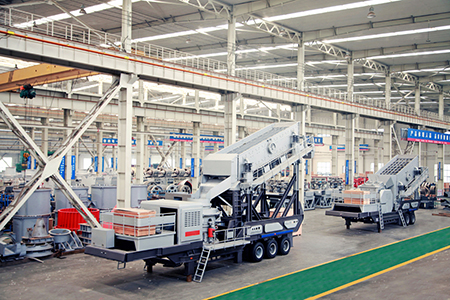
Optimization of Cement Grinding Operation in Ball Mills PEC ...
Several energy efficient options for cement grinding are available today such as vertical roller mills, roller presses (typically in combination with a ball mill), and clinker pre-grinders with ball mills. Ball mills have been the traditional method of comminution in the mineral processing industries and continue to operate with old generation ...
More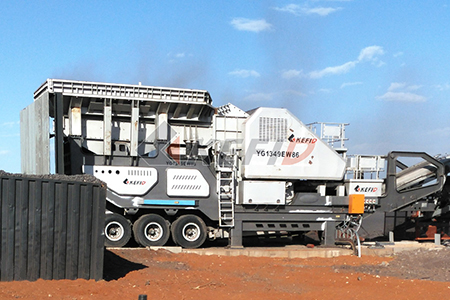
The Decision Algorithm of Cement Mill Operation Index Based
2023年1月25日 Abstract An improved differential evolutionary cement mill operation index decision algorithm based on constraint control and selection strategy is proposed to address the problem that the operation index is usually decided by manual experience in the cement mill operation process, which causes unqualified cement specific surface area and excessive
More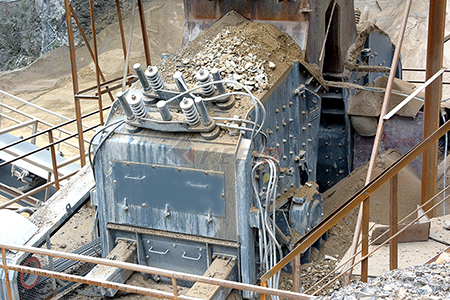
OPTIMIZATION OF CEMENT GRINDING OPERATION IN BALL MILLS
OPTIMIZATION OF CEMENT GRINDING OPERATION IN BALL MILLS Several energy efficient options for cement grinding are available today such as vertical roller mills, roller presses (typically in combination with a ball mill), and clinker pregrinder- s with ball mills. Ball mills have been the traditional method of comminution in the mineral processing
More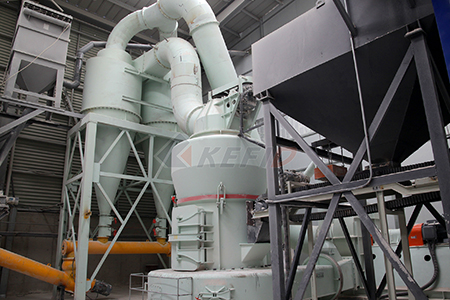
Cement Mill Optimization: Practical Strategies for Enhanced
Optimizing ball mill internals: The internal design of the ball mill, including the diaphragms, liners, and grinding media, can also impact the grinding efficiency. Using high-quality grinding media, optimizing the diaphragm design to improve ventilation, and regularly inspecting and replacing worn-out liners can result in up to 15% reduction in specific energy consumption and
More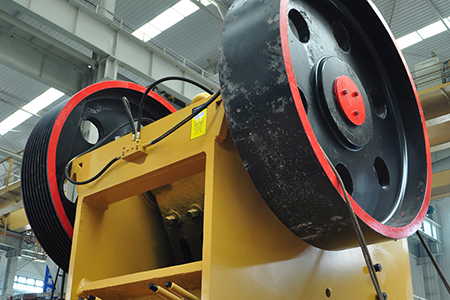
[PDF] The selection and design of mill liners - Semantic Scholar
Examples of good and bad liner design are given, followed by a rigorous approach to liner design based on the best technology available, combined with experience and logical engineering thinking. Methods of monitoring the progressive wear of liners, and relating this to the performance of the mill are presented.
More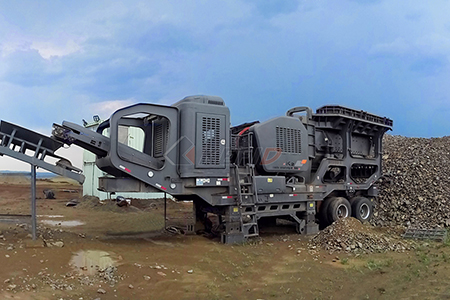
Energy and exergy analyses for a cement ball mill of a new
2020年2月1日 Rather than huge expansion, most industries will focus on maximizing resources for maximum pro tability. Consequently, a study of the impact of operational parameters on ball mill energy e ciency ...
More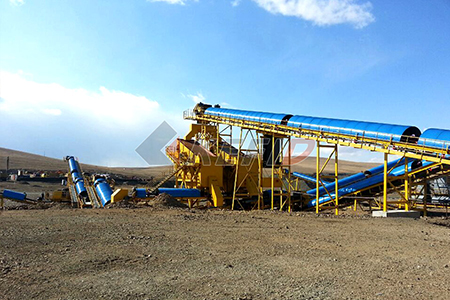
Failure analysis of a ball mill located in a cement’s production line
2022年8月1日 The ball mill understudy has a length of 13.07 m in its cylindrical geometry and a length between supports of 16.2 m (Fig. 1 a,b).The formation of cracks in the middle span has been identified, generally spreading from the holes near the maintenance manhole, as shown in Fig. 1 c. Certified welders carry the repairing procedure using PERMA 622 electrodes [1].
More- organigramme de fabrication de roches concassées
- broyeur machine dextraction de minerai de chrome à vendre maroc
- concasseur a beton portable a louer qatar
- la conception du système broyeur
- broyeurs de vilebrequin à vendre en afrique du sud
- broyeur de revêtement fabriqué au Pakistan
- broyeurs de charbon des centrales électriques images
- concasseur occasion en pierre vendre
- fournisseur battoirs pour station de concassage en algerie
- économie des concasseurs
- or concasseur de minerai moulin le co
- ofertas de trabajo carrire
- mini broyeur de décombres à vendre
- paramètre de maintenance de l usine concasseur
- concasseur à cône utilisé en australie