ball milling particle size

Phone
+86 15538087991


Location
No. 201 Huaxiasanlu road, Pudong, Shanghai, China
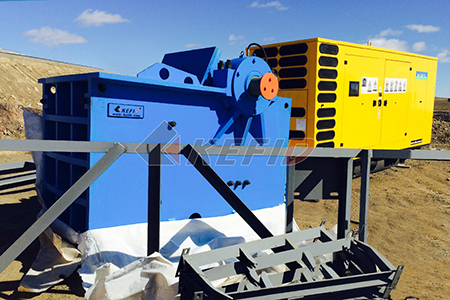
Effect of ball and feed particle size distribution on the milling ...
2018年6月1日 In this article, alternative forms of optimizing the milling efficiency of a laboratory scale ball mill by varying the grinding media size distribution and the feed material particle size distribution were investigated.
More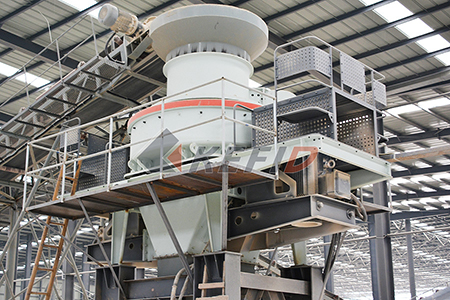
Effects of Ball Size on the Grinding Behavior of Talc
2019年10月31日 In this study, we investigate the effect of the ball size in a high-energy ball mill on the comminution rate and particle size reduction.
More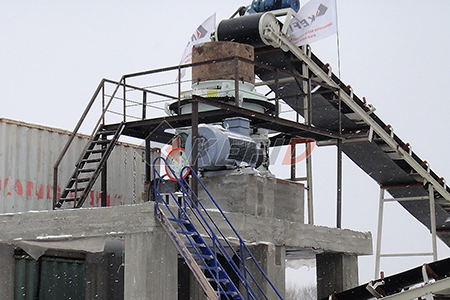
Effect of Milling Parameters on Size, Morphology, and Structure
2022年9月20日 In this work, the evolution of the size and morphology of Fe-Ga particles during vibration ball milling is documented and discussed. Low intensity (12 Hz) and high intensity (20 Hz) of milling with different ball-to-powder ratios (2:1 and 5:1) are used. A systematic study of the effect of various milling parameters on the size and morphology of particles is carried out
More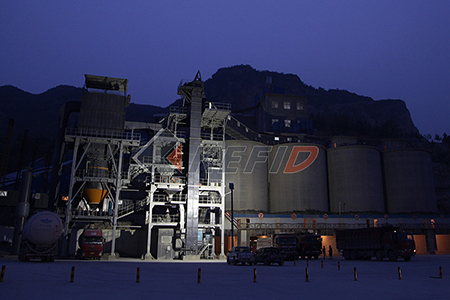
Ball Milling - an overview ScienceDirect Topics
Ball milling: The main principle of mechanical milling can be described as the exploitation of high energy grinding to reduce the particle size. In general, the high energy ball milling route is used to yield nanosized particles, especially for metallic PNPs synthesis [45].
More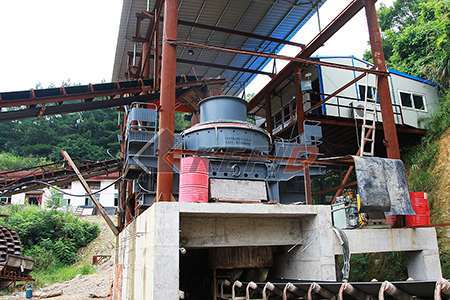
Calculate and Select Ball Mill Ball Size for Optimum
2013年8月3日 In Grinding, selecting (calculate) the correct or optimum ball size that allows for the best and optimum/ideal or target grind size to be achieved by your ball mill is an important thing for a Mineral Processing Engineer AKA
More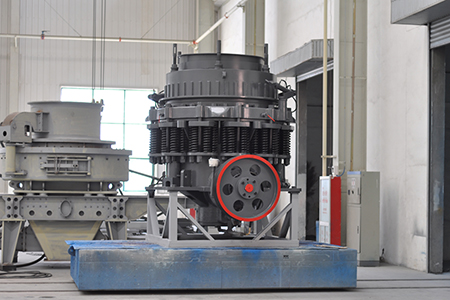
Selected Advances in Modelling of Size Reduction in Ball Mills
2023年9月22日 For the ball milling operation, the influence of particle size distribution on the grinding kinetics is also well-known now [8, 14, 23, 24, 34, 35]. Attention should be paid to these factors while designing experiments for developing quantitative correlations for mill scale-up design work. 4.1 Mill Diameter Scale-up
More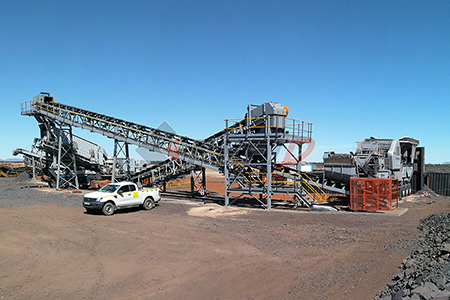
Exploring the relationship between solvent-assisted ball milling ...
2021年2月1日 Garnet-type solid electrolytes, such as Li 6.4 La 3 Zr 1.4 Ta 0.6 O 12 (LLZTO), are promising materials for solid-state batteries, but processing remains a challenge, in part due to the high sintering temperature required for densification. This temperature can be lowered by decreasing the initial particle size via solvent-assisted ball milling, but the relationship
More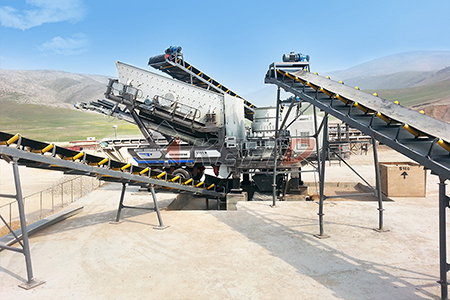
Ball mill - Wikipedia
A section cut-through of ball mills. A ball mill is a type of grinder filled with grinding balls, used to grind or blend materials for use in mineral dressing processes, paints, pyrotechnics, ceramics, and selective laser sintering.It works on the principle of impact and attrition: size reduction is done by impact as the balls drop from near the top of the shell.
More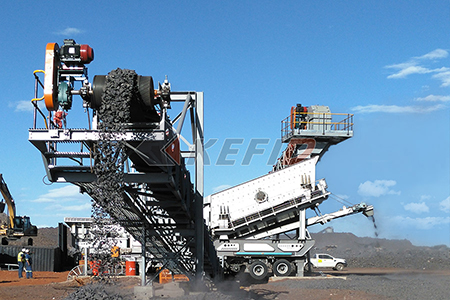
Evolution of grinding energy and particle size during dry ball-milling
2020年10月1日 The particle size distribution was determined by Laser Diffraction (LD) using a Mastersizer 2000 (Malvern Instruments Ltd., ... with the results of Schellinger 1951 for the ball milling of silica sand [29]. Interestingly, this value was determined from a comparison between the dissipated thermal energy (obtained by calorimetry) ...
More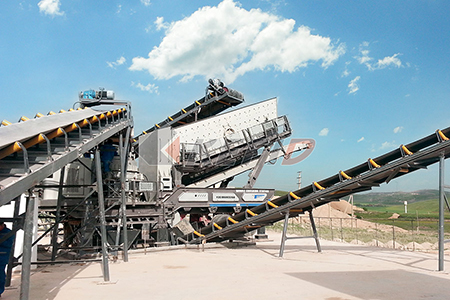
Effect of ball size and powder loading on the milling efficiency
2013年12月1日 Effect of ball milling parameters on the particle size in nanocrystalline powders. Technical Physics Letters, 33 (2007), pp. 828-832. View in Scopus Google Scholar [10] D. Guerard. Ball milling in the presence of a fluid: results and perspectives. Reviews on Advanced Materials Science, 18 (2008), pp. 225-230.
More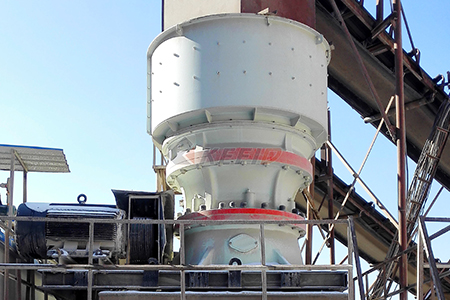
Effect of ball and feed particle size distribution on the milling ...
2018年2月1日 In another study to investigate ball size distribution on ball mill efficiency by Hlabangana et al. [50] using the attainable region technique on a silica ore by dry milling, a three-ball mix of ...
More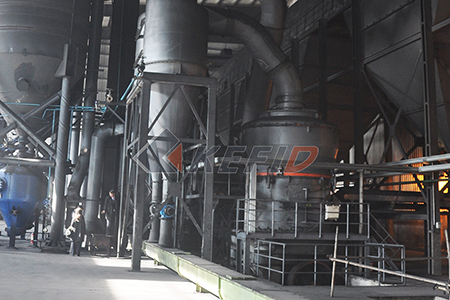
Effect of ball size and powder loading on the milling efficiency
2013年12月1日 There have been investigations on the influences of parameters associated with grinding balls such as ball size distribution [4], [5] and ball shape [6] on the particle comminution. Salili et al. [7] reported the importance of the small ball size and small mass ratio of powder to ball for the efficient ball mill, while only two sets of experimental data for these variables were
More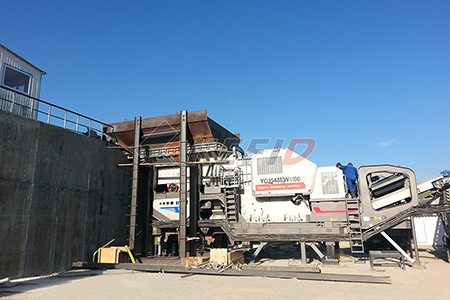
Ball Mill - an overview ScienceDirect Topics
The ball mill is operated in closed circuit with a particle-size measurement device and size-control cyclones. The cyclones send correct-size material on to flotation and direct oversize material back to the ball mill for further grinding.
More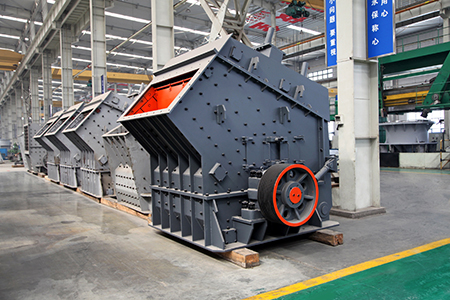
Ball Milling Powder Processing 30 Years of Expertise at AVEKA
With this motion, the particles in between the media and chamber walls are reduced in size by both impact and abrasion. In ball milling, the desired particle size is achieved by controlling the time, applied energy, and the size and density of the grinding media. Download the Grinding and Classification flyer here
More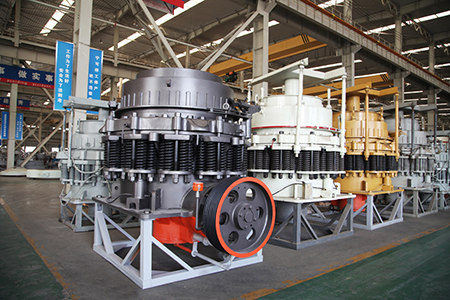
Effect of ball and feed particle size distribution on the milling ...
Effect of ball and feed particle size distribution on the milling efficiency of a ball mill: An attainable region approach N. Hlabangana a, G. Danha b, *, E. Muzenda b a Department of Chemical Engineering, National University of Science and Technology, P O Box AC 939, Ascot Bulawayo, Zimbabwe b Department of Chemical, Materials and Metallurgical Engineering,
More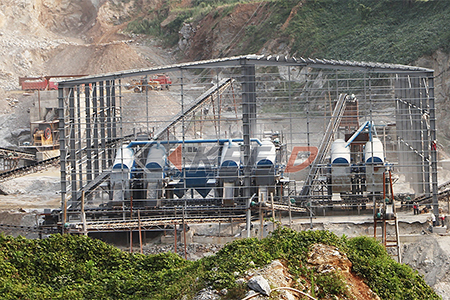
Ball Milling of Amaranth Starch-Enriched Fraction. Changes on Particle
2014年2月23日 Ball-milling procedure affects particle size of starch-enriched fraction flours, achieving higher size reduction with higher employed energies. The flour produced at the higher milling energy (6.52 kJ/g) and having a mean size of
More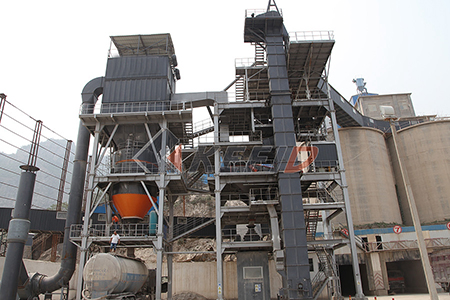
Investigating the effect of process variables for ball milling of
2024年1月11日 Finally, D 10, D 50 and D 90 particle size parameters were calculated by Eq. 3 for individual experimental runs, changing the F value accordingly. As the most representative value, particle size D 50 was used for further modelling steps.. 2.3 Milling experiments. Size reduction of biomass was carried out using a Drum Mill TM 300 (Retsch Ltd., Haan, Germany).
More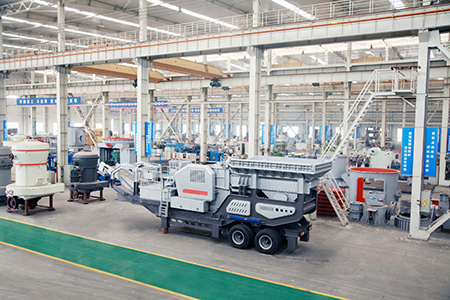
Grinding in Ball Mills: Modeling and Process Control
2012年6月1日 Besides particle size reduction, ball mills are also widely used for mixing, ... efficiency of the ball mill and the economic assessment of the process control. R e f e r e n c e s . 1.
More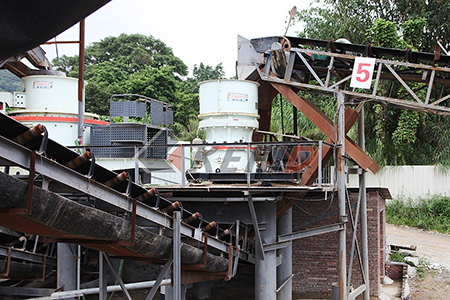
Powder Ball Milling: An energy balance approach to particle size
Ball milling, limiting particle size, Rittinger’s law, energy density, specific surface energy, JMAK kinetics. Abbreviations ... At a particle size of less than 20 μm, milling studies exhibit a progressive departure from a linear energy-surface dependence. This divergence is
More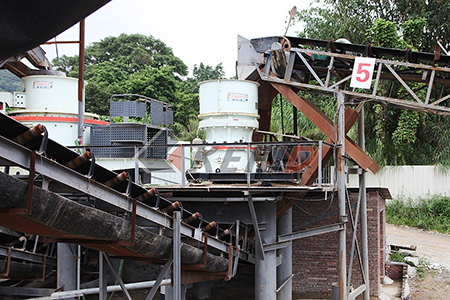
Ball Milling Guide - Inoxia
Particle size. Ball milling has been used to grind materials to average particle sizes of 20 nanometres and finer, with extended milling time continuing to reduce particle size but with diminishing returns. Some materials may start to cake and will require additives to
More>> Next: Machine De Minerai D Or De Granit Canada
- usine de traitement particulier de cuivre dubai et uae
- Raymond moulin trieuse
- machines de criblage électro dermique
- raymond calcaire de concassage
- machine stone crusher in malaysia
- petit co t pierre de l usine de broyage en inde
- recyclage du béton concassage de granulats grossiers
- tuiles de carrières au nigeria
- vsi 200 prix de tph 200 tph co
- parties d n concasseur de minerai de fer
- Spart partie cône arabie mâchoire concasseur cs 3 pi
- opération de concasseur à mâchoires pdf
- de martelo de segunda mão à venda África do sul
- usine de broyeur de minerai de fer 224 koira odisha
- concasseur de pierre fiable broyeur de processus de silice